Stainless steel flanges are widely used in the petroleum industry, water and natural gas pipelines, most of which are under corresponding pressure. This kind of thin bellows is generally welded process, because it is too thin, about 0.2 mm, difficult to weld process.
The welding process includes welding, brazing, etc. The arc welding process of 304 stainless steel flanges or other pipelines means that the arc can not directly point to the bellows, but is arc hot melt welding on the bellows.

Preparation before welding process
Remove oil and other dirt from stainless steel corrugated flange. Assuming the welding process flange and leakage, the original welding process scars should be eliminated, the straight pipe of the flange should be polished and polished metal luster, the straight pipe of the bellows is too thin and can not be polished, ground and cleaned, and the light should be polished and polished with a manual emery cloth.
Welding process assembly: The fusion treatment implementation can be stacked on the straight pipe surfacing layer of the flange pipe, and the production is 0~0.05 mm open space or manual grinding.
Arc forward in the flange tube is essential. Arc refers to a very thick pipeline, the use of arc flame heating bellows, plug the edge of the bellows with welding wire, melt stainless steel welding wire melt bellows, should be welded process thick wall pipe, select short welding or spot welding.
In the welding process, the melting standard of the bellows should be consulted at any time. Under normal circumstances, 1 time should melt 1 or 3 molten pools, so it is not suitable for 1 time 1 welding process. Especially in the case of large open space, it is very easy to burn through.
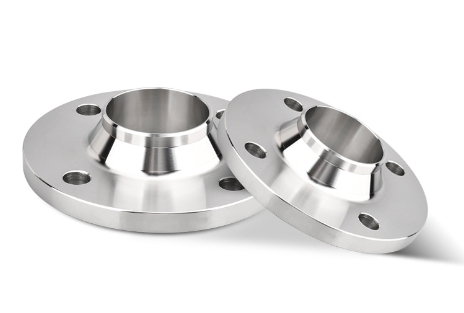
According to the site, when the flange and the cylinder are welded together, the riveting operator does not apply the restraint tool to prevent welding deformation of the flange. For the flange and cylinder welding structure, it is not an easy thing to control the welding deformation without restraint tooling.
Because the welded structure can be approximately single-sided continuous welding, during the welding process, the axial heated part of the weld area is affected by the circumferential contraction stress during the cooling of the weld, and the overall temperature of the flange also increases with the distance from the heat-affected zone of the weld, the lower the temperature and the greater the rigidity. It is easy to make the lower end of the flange contract circumferentially towards the central axis of the flange, and thus produce angular deformation.
In addition, many manufacturers have welding operators fail to perform welding operations in strict accordance with the manufacturing process procedures and welding parameters, often welding the workpiece solely based on welding experience and operating habits, therefore, to a large extent, directly affect the quality of welding.