Neck flat welded flange is produced by carbon fiber processing, the main application is used as a pipe network, and connect it to the end of the pipe a common kind of pipe fittings. In addition, it has a flange for the equipment inlet and outlet position, which is used to connect two devices.
Flange processing with neck flat welding
This kind of pipe fittings after a certain thermal treatment deformation, based on metal material deformation and recrystallization, will cause the original thick dendritic crystal and columnar crystal gradually into a small, symmetrical equiaxial structure
At the same time, there will be a phenomenon of recrystallization arrangement, so that the organizational structure of the raw material is more closely aligned with the appearance of the forging, and the metal material flow line is more complete, which can effectively ensure that the workpiece has better mechanical properties and a long application life.
This kind of pipe fittings can be given very good practical effects after being processed by fine forging, cold extrusion, warm molding and other processes. When connected with the pipeline, some of the pump and valve body of the equipment are connected with it, which can be called flange connection.
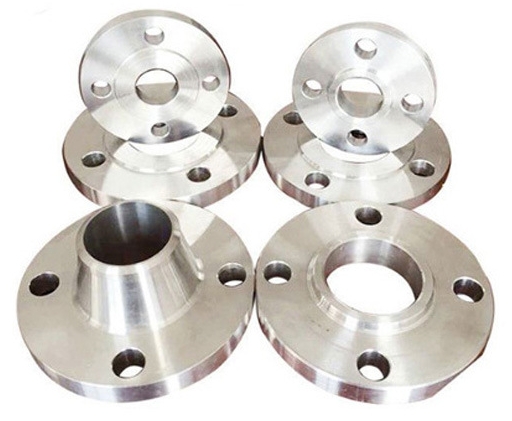
The neck flat welded flange has both neck and round pipe transition, so as to be welded with the pipe. It can be divided into two categories: low voltage small caliber and high voltage large caliber. At the same time, using welded flange pieces, the wall thickness of pipe fittings under different pressures, the caliber and number of connecting bolts will also be different.
Manufacturing technology of flat welding flange with neck
In the production and manufacturing links, we must comply with certain process technical parameters and regulations to operate, and effectively ensure that the application can be followed by the correct method and mechanism, so that the quality of the pipe network can be strictly rigorous in the application.
As a common type of joint seal, the locking force of the bolt must be relatively large. And if you want to achieve this, the bolt must be bigger.
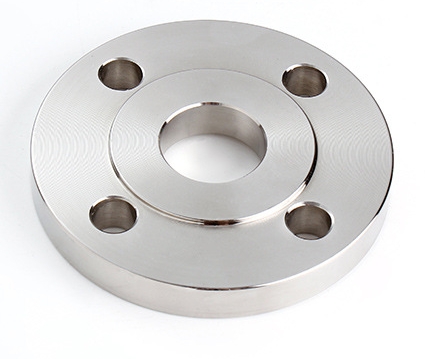
However, it should be noted here that the larger the diameter of the bolt, the higher the probability of bending deformation of the connecting flange, the only way we can do this is to increase the wall thickness of the flange position.
In addition, from the practical application and the original design point of view, the neck flat welding flange stipulates that 50% of the bolt load is used as the extrusion gasket, and the load used as the connecting pressure is the remaining 50%.