The flat welding flange with neck is because the neck angle is lower, the bending stiffness and load-bearing capacity of the flat welding flange with neck are gradually improved, and it is more convenient to assemble on site and is more popular among people. It is a more commonly used flange type.
So, do you know which parts the neck flat welding flange is composed of? What is the basic principle of neck flat welding flange? Next, the editor will briefly introduce the neck flat welding flange to everyone so that everyone can understand it more easily.
Principle of flat welding flange with neck
Before understanding the basic principles of the neck flat welding flange, we first answer the previous question, that is: which parts of the neck flat welding flange are combined, in other words, the structure of the neck flat welding flange, with The neck flat welding flange contains a flange piece, an inner hole is opened in the center of the flange plate, and the flange plate is also equipped with numerous screw holes.
One side of the flange is equipped with a neck-shaped boss. The inner diameter of the neck-shaped boss is the same as the inner diameter of the inner hole and is connected to each other. The other side of the flange is equipped with an annular indentation. The center of the annular indentation is aligned with the central axis of the inner hole. Overlap, the radius of the annular dent is larger than the radius of the inner hole, and there is also an annular dent inside the annular dent. The center of the annular dent overlaps with the central axis of the inner hole, and the outer layer of the annular dent overlaps with the annular dent. The outer layers overlap.
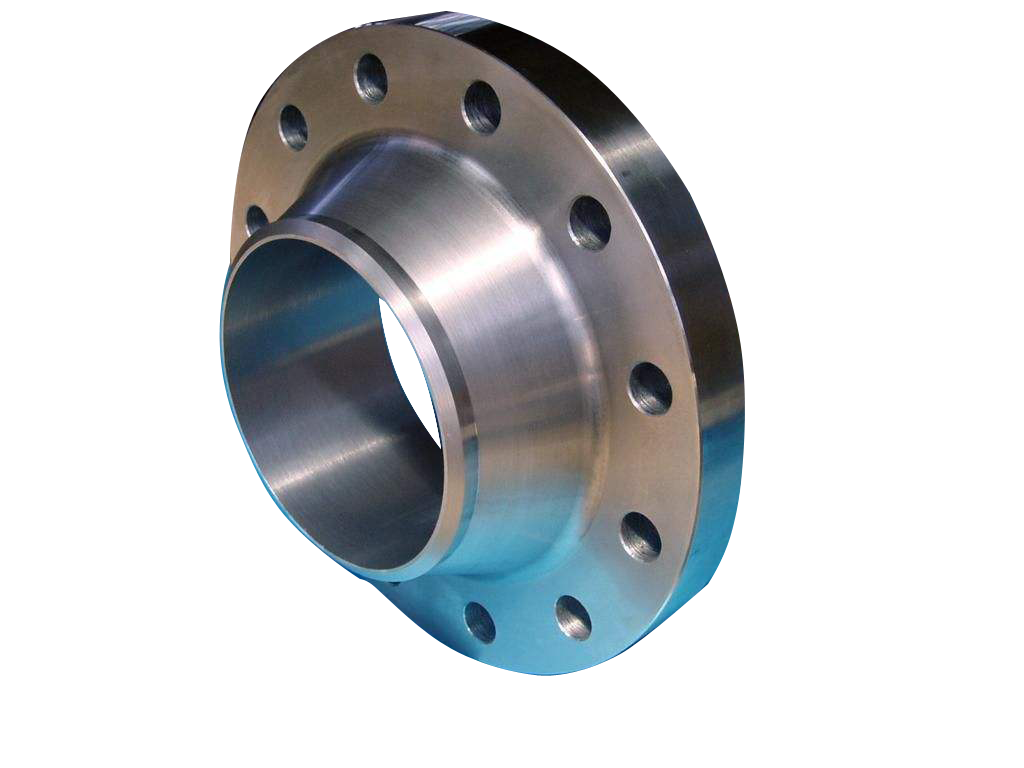
However, there are many problems with the flat welding flange with a neck, namely: compared with the butt welding flange, the flat welding flange with a neck has a large welding workload, high consumption of welding rods, and cannot withstand high temperatures, repeated bending and temperature. ups and downs. Moreover, the cost is higher than that of plate-type flat welding flanges. Due to its style characteristics, it is more likely to be bruised on the transportation road. This is why everyone needs to pay special attention when choosing neck flat welding flanges.
How can you tell the quality of neck flat welding flange?
This is a question that many customers are concerned about. Here are five ways to teach you how to accurately select high-quality products.
Comparing the quotation, among the flanges on the market, the forged flange is the cheapest, followed by the cast and forged flange, and the purely forged flange has the highest quotation.
Do destructive tests and separate the flanges. The forged ones have trachoma but the pure forged ones do not. Cast-forged flanges sometimes have cracks.
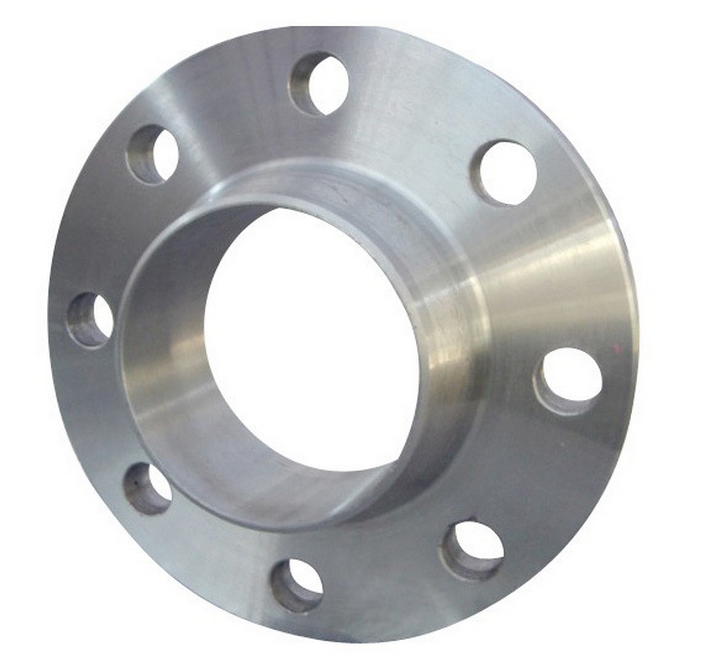
From the flange dimensions and surface finish, forged flanges usually have negative dimensions of 1-5mm, irregular edge chamfers, and burrs in the holes that are not smooth, while forged flanges have smaller dimensions.
Weighing the weight, for flanges of the same size, the forged ones will be lighter than the forged flanges.
Choose based on suppliers, preferably manufacturers. With quality assurance