What is the difference between ASTM A234 flange and A105?
What is the flange rating A105?
For carbon steel A105 flanges, common pressure-temperature ratings and classes are specified in standards such as ASME B16.5. Here’s a simplified table outlining some common flange classes and pressure-temperature ratings for A105 carbon steel flanges:
Flange Class | Pressure-Temperature Rating (psig) |
---|---|
150 | 285 at 100°F, 260 at 500°F |
300 | 740 at 100°F, 660 at 500°F |
600 | 1480 at 100°F, 1305 at 500°F |
900 | 2220 at 100°F, 1950 at 500°F |
1500 | 3705 at 100°F, 3265 at 500°F |
2500 | 6170 at 100°F, 5425 at 500°F |
Note: The values in the table are indicative and may vary. Always refer to the specific standard (e.g., ASME B16.5) and consult with relevant engineering codes to determine the precise pressure-temperature ratings for a given flange class and material grade. The pressure-temperature ratings are typically specified for a range of temperatures, and the values provided in the table represent only a snapshot at specific temperatures.
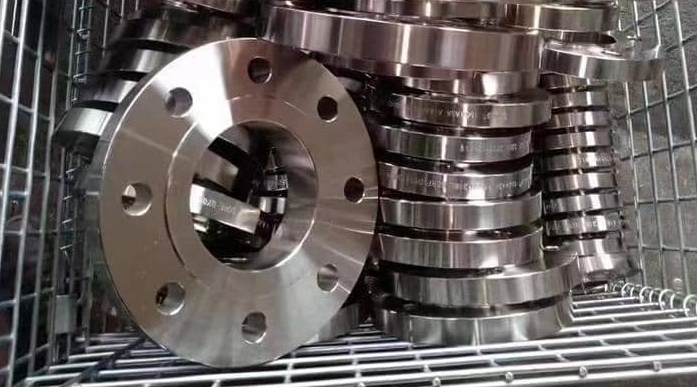
What is the difference between ASTM A234 flange and A105?
ASTM A234 is a standard specification for alloy steel and stainless steel butt-welding pipe fittings. It encompasses various types of welded pipe fittings, including elbows, tees, reducers, and other components. This standard is applicable to piping systems used in industries such as chemical, petroleum, natural gas, and power generation, especially in high-temperature and high-pressure environments.
ASTM A105 is a standard that covers carbon steel forgings for piping applications. It primarily includes carbon steel flanges, flanged fittings, valves, and similar components for high-temperature and high-pressure services. A105 is commonly used for manufacturing flanges rather than butt-welded pipe fittings

Therefore, the key distinction between these two standards lies in their coverage.
ASTM A234 primarily addresses alloy steel and stainless steel butt-welding pipe fittings, while ASTM A105 focuses on carbon steel forgings, commonly used in the manufacture of flanges.
The differences encompass material composition, manufacturing processes, and the intended applications in piping systems. The choice between the two depends on the specific requirements of the application and the piping system.