A Comprehensive Guide to Understanding Sliding Flanges in Industrial Environments
In the complex landscape of industrial piping systems, sliding flanges play a pivotal role, facilitating the seamless connection of pipes. This guide aims to provide a comprehensive understanding of sliding flanges, exploring their functionality, applications, and key considerations in industrial environments.
Functionality of Sliding Flanges: Sliding flanges, also known as slip-on or expansion flanges, are engineered to allow controlled axial movement along the pipe axis. This unique design enables flexibility in accommodating thermal expansion, contraction, and vibrations within industrial piping systems, preventing stress and potential damage to the system.
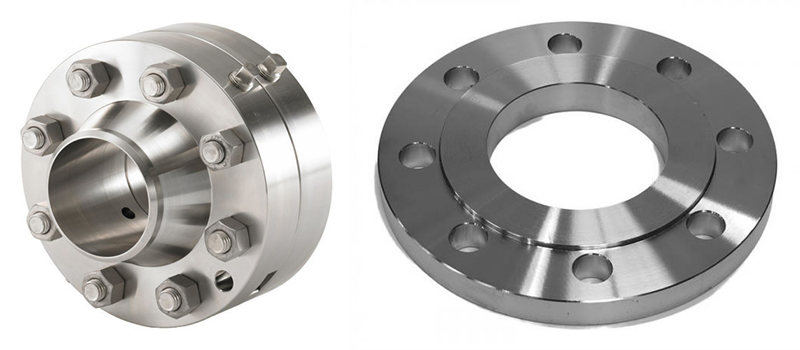
Applications Across Industries: Sliding flanges find applications across diverse industries, including oil and gas, chemical processing, and power generation. Their versatility makes them suitable for environments where temperature variations, dynamic forces, and stress on piping systems are common occurrences, highlighting their importance in ensuring the reliability of critical infrastructure.
Material Selection for Durability: The choice of materials for sliding flanges is crucial in ensuring durability and longevity. Selecting materials with corrosion resistance and temperature tolerance is essential, as these factors contribute to the overall resilience of the flanges in demanding industrial environments, reducing maintenance needs and extending their operational life.
Installation Considerations: The installation of sliding flanges requires precision to ensure optimal functionality. Proper alignment and secure attachment to the pipe are critical to enable smooth axial movement. Attention to these details during installation sets the foundation for efficient performance and reliable operation throughout the flange’s service life.
Mitigating Wear and Tear: Regular wear and tear are inevitable in industrial environments, but strategic measures can be taken to mitigate their impact on sliding flanges. Implementing surface finishes and lubrication techniques helps minimize friction during movement, reducing wear and ensuring the longevity of the flanges in challenging operating conditions.
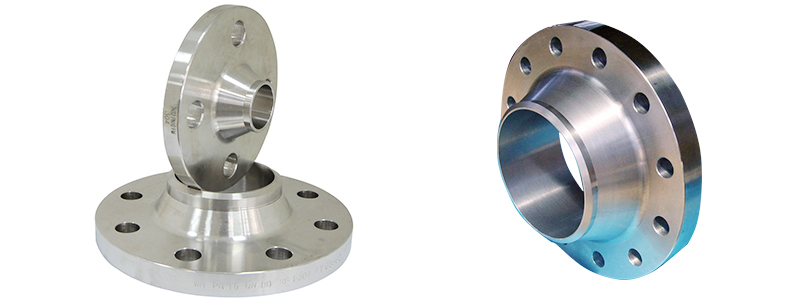
Maintenance Practices for Longevity: A proactive maintenance approach is essential to maximize the longevity of sliding flanges. Regular inspections for signs of corrosion, misalignment, or wear allow for timely interventions, preventing potential issues and ensuring that the flanges continue to function optimally within the industrial system.
Conclusion: In conclusion, a solid understanding of sliding flanges is imperative for engineers and professionals working in industrial environments. Recognizing their functionality, selecting appropriate materials, and implementing effective installation and maintenance practices collectively contribute to the reliable and efficient performance of sliding flanges in diverse industrial settings.