Sliding flanges, crucial components in industrial piping systems, can be optimized to improve overall efficiency. By implementing strategic measures and considering key factors, the performance of sliding flanges can be elevated, contributing to smoother operations and increased reliability in diverse industrial applications.
Material Selection for Durability: Choosing the right materials for sliding flanges is paramount to enhance durability and longevity. Opting for corrosion-resistant alloys or coatings ensures that the flanges withstand harsh environmental conditions, contributing to a prolonged service life and reduced maintenance requirements.
Precision Machining for Seamless Fit: Precision machining plays a crucial role in ensuring a seamless fit of sliding flanges. Tight tolerances and accurate machining contribute to optimal alignment, reducing the risk of misalignments during installation and enhancing the overall integrity of pipe connections.
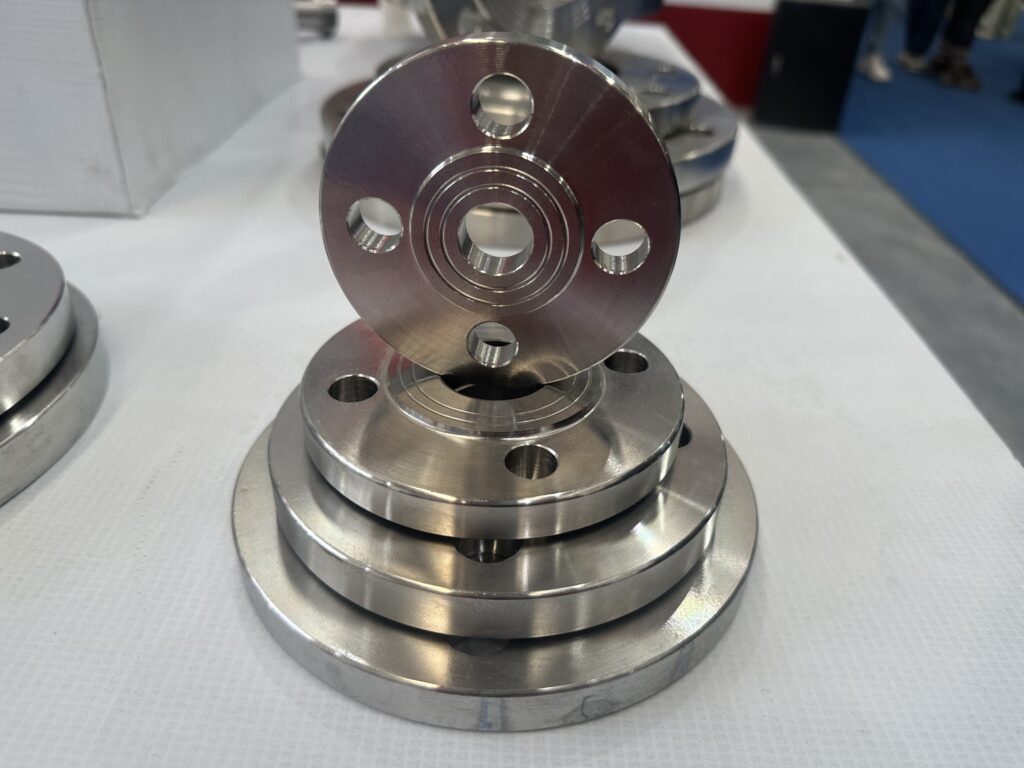
Surface Finishing for Reduced Friction: Applying smooth and corrosion-resistant surface finishes to sliding flanges reduces friction during movement. This not only improves the ease of sliding but also minimizes wear and tear, contributing to a more efficient and reliable operation over time.
Regular Inspection and Maintenance: Implementing a proactive inspection and maintenance schedule is essential for ensuring the efficiency of sliding flanges. Regular checks for signs of wear, corrosion, or misalignment allow for timely interventions, preventing potential issues and extending the operational life of the flanges.
Proper Lubrication for Smooth Movement: Ensuring proper lubrication of sliding flanges is a key factor in optimizing their efficiency. Lubricants reduce friction, allowing for smoother movement and minimizing the chances of binding or resistance during operation. This simple yet crucial step contributes to overall system reliability.
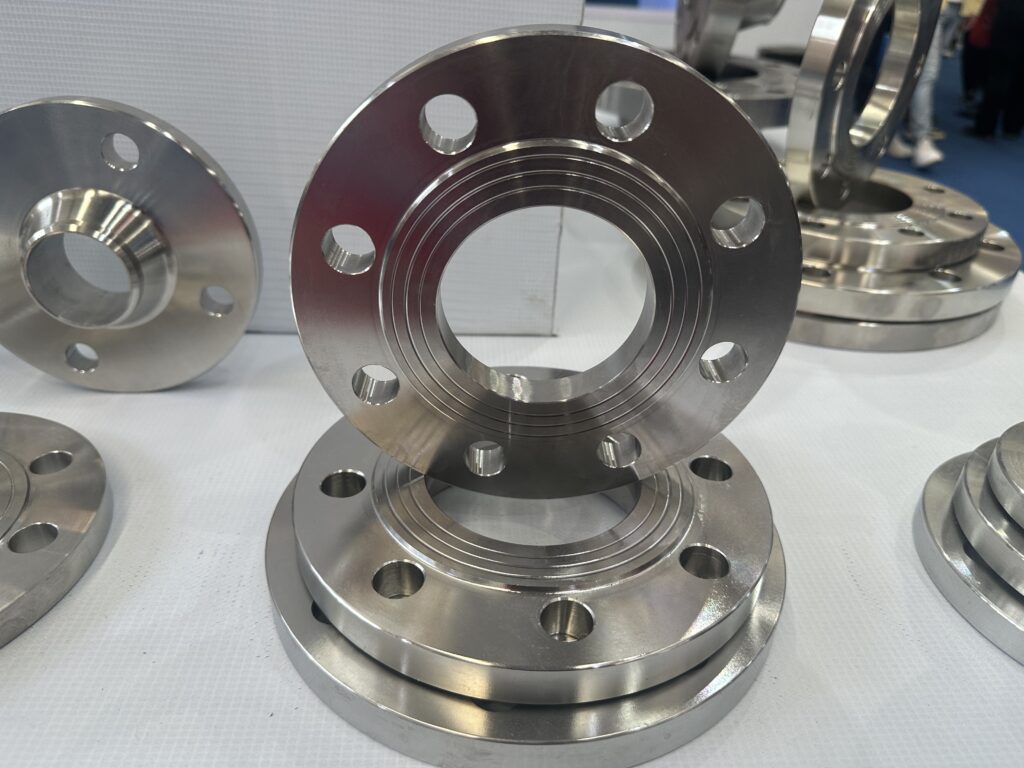
Consideration of Thermal Expansion: In applications where thermal expansion is a factor, accounting for this phenomenon is crucial for improving sliding flange efficiency. Allowing for controlled movement and implementing expansion joints or flexible connectors helps mitigate stress on the flanges and ensures consistent performance under varying temperatures.
Conclusion: In conclusion, optimizing the efficiency of sliding flanges involves a holistic approach, from material selection and precision machining to regular maintenance and proper lubrication. By addressing these aspects, industrial systems can maximize the performance of sliding flanges, contributing to enhanced reliability and overall operational efficiency.