Stainless steel flanges serve as pivotal components in the construction and functionality of piping systems, providing essential connections and terminations. The diversity of applications across various industries necessitates a nuanced understanding of the different types of stainless steel flanges available. This article aims to provide a comprehensive overview of the various types, their unique characteristics, and the specific applications for which they are best suited.
1. Weld Neck Flanges: Characteristics: Weld neck flanges feature a long, tapered hub that facilitates high-integrity welding to the adjoining pipe. This design enhances structural strength and provides resistance to deformation under high-pressure applications. Applications: Commonly employed in high-pressure and high-temperature services such as oil and gas pipelines, chemical processing, and power generation.
2. Slip-On Flanges: Characteristics: Slip-on flanges have a bore slightly larger than the outer diameter of the pipe, allowing for easy slip-on installation. They are secured with fillet welding on both sides. Applications: Ideal for applications with less stringent requirements on strength, commonly found in low-pressure and non-critical services.
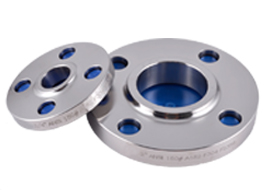
3. Blind Flanges: Characteristics: Blind flanges are solid disks that cover or close the end of a pipe, acting as a termination point. They are often used to seal the end of a pipeline or pressure vessel. Applications: Employed in systems where future access to the pipeline is not required, or where the pipe needs to be closed off securely.
4. Lap Joint Flanges: Characteristics: Lap joint flanges consist of two parts – a flat, stub-end and a loose backing flange. This design facilitates easy alignment and bolting, allowing rotational adjustment. Applications: Suitable for systems requiring frequent dismantling or maintenance, such as chemical processing and food industries.
5. Socket Weld Flanges: Characteristics: Socket weld flanges have a socket or a female end into which the pipe is inserted. Fillet welds on the outer side provide additional strength. Applications: Commonly used in small-diameter, high-pressure pipelines and where the fluid flow does not necessitate full bore opening.
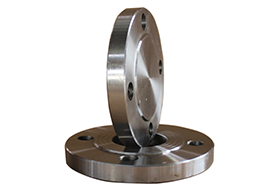
6. Threaded Flanges: Characteristics: Threaded flanges have threads on the bore, enabling them to be connected to pipes with matching external threads. They provide ease of installation and are suitable for low-pressure applications. Applications: Frequently utilized in plumbing and low-pressure applications where welding is not preferred or feasible.
7. Orifice Flanges: Characteristics: Orifice flanges are specifically designed for orifice metering of gas or liquids. They feature pairs of pressure tappings for accurate flow measurement. Applications: Widely used in oil and gas industries, petrochemical plants, and other applications requiring precise fluid measurement.
In conclusion, the diverse array of stainless steel flanges caters to the specific needs of various industries. Understanding the characteristics and applications of each type is essential for selecting the most suitable flange for a given piping system, ensuring optimal performance and longevity.